A Treasure Chest of Late-Nineteenth-Century Tools: John E. Kraus’s Tool Chest
- marcsitkin
- Mar 25, 2021
- 15 min read
Updated: May 4, 2023
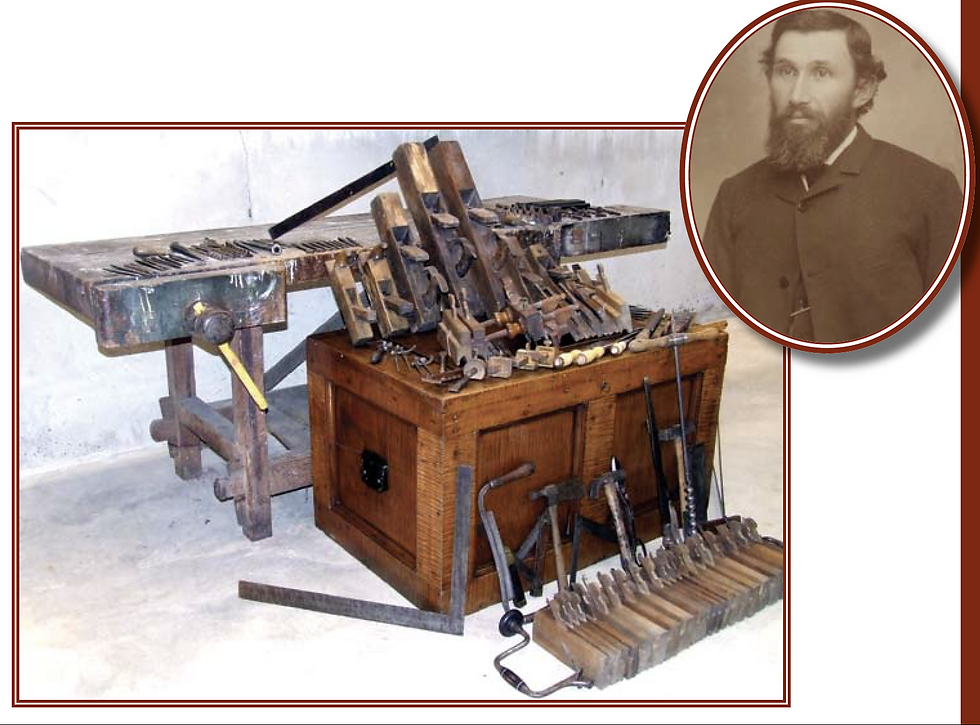
Excerpted from The Chronicle Vol. 60 no. 3, September 2007
by Jeff Neil
Upon returning from a quilting “camp” my wife told me that she had passed my e-mail address along to a woman whose husband had some “old tools” that he was trying to find a home for. The next day, I received an e-mail from John Kraus, Jr., with some photographs of his tools (Figure 1). I was struck speechless looking at the photographs of a largely intact chest of tools that had been owned by his great-grandfather, John Erhard Kraus, and used by him as a professional woodworker in Syracuse, New York, beginning in the 1870s.

Figure 1. A view inside the tool chest showing the molding planes in the bottom back till, the bench planes in the center till, and one sliding till containing some of the other tools. The saw till is located in the bottom front, shielded from view in the photo.
As an amateur woodworker, seeing the photographs was like looking into a treasure chest. Or, more correctly, it was like looking through a window into the life and times of a craftsman during the waning days of the wooden plane when it was still the professional’s tool of choice over the newfangled metal ones.
I was able to acquire this tool chest complete with tools, and as a bonus I was also given the workbench that John E. Kraus used. I have learned a great deal about the man, his life, and the tools of his trade, and I expect to continue to learn more.
Let’s open this “treasure chest” of tools and look back in time.

Figure 2. A stack of twenty wooden hollows and rounds from the tool chest, all made by D.R. Barton & Co. in Rochester, N.Y.
The Original Owner John Erhard Kraus was a twenty-eight-year-old Bavarian army veteran when he arrived in Syracuse in 1869. In 1871 in Syracuse, he married a Civil War widow (whose first husband was killed at the Battle of Lookout Mountain). He began his career probably as a jointer or interior finish carpenter within the large German community in that city. He had most likely been trained in his profession as a woodworker in Bavaria before his army service in the Austro-Prussian War of 1866, and his tool chest still contains three German wooden planes from his earlier life. His first job in Syracuse was as part of a team of three who finished the interior of the newly built Salem Evangelical Church in Syracuse. According to a history of the church published that year, Kraus joined that congregation and remained an active member until at least 1907.(1) His name appears in the Syracuse city directories from 1873 to 1883 as a carpenter and in 1884 and later as a “contractor.”(2) The mixture of tools in the chest seems consistent with interior finish work, although he also constructed some furnishings, at least for his own family.
Kraus is remembered in family lore as a practical and frugal man. That frugality is reflected in an oak pedestal desk, attributed to him and still owned by his family. The top and sides of the desk have been cleverly made using leftover oak flooring boards. The steel stamp Kraus used to mark his tools was included in the chest, and it also suggests frugality. In Kraus’s initial listings in the Syracuse city directories from 1873 to 1876, his first name is recorded as Erhardt or Erhard. In 1880 and later, the directory changes and Kraus is listed with a first name of John with “E” as a middle initial. The stamp and his tools, however, are all marked “A. Kraus.” There could be several explanations for this discrepancy, but my theory is that he when he ordered the stamp, he verbally gave his name to the supplier as Erhard Kraus, which perhaps the vendor assumed from German pronunciation began with an “A” and not an “E.” It appears that rather than buy another stamp with the correct initials, he just used the one he had received.
Carpenter/Contractors in the Second Half of the Nineteenth Century A review of life as a carpenter in the second half of the nineteenth century was published by the journal National Builder in 1914. “Memories of Fifty Years Ago in The Building Trades” provides some insights into the working environment, methods of work, and the tools used by carpenters in that period.(3)

Figure 3. Five beading planes, two skew rabbet planes, a nosing plane, a casing plane and a plow plane.
“The ten-hour day was first in vogue in 1850 in towns and cities, but in the country a day was from daylight until dark. But no fault was found if you were off work an hour now and again. I have known all the men on the job, boys and all, to leave the work to run to a dog fight and stay off for an hour or more —the boss, too! No grumbling followed. Things were hard for the boys, and yet things were comfortable, made so by the fire and easy surroundings at home. Those days were the happiest of my life, and if I had to live over again, I would like nothing better. It was hard work, but the rest was more delightful and more than made up for the stress.
“Good framers were always in demand and their wages were from $1.75 to $2.25 per day with board.
“With regard to wages, at this distance they look small; but it seems to me that the buying power of a day’s wages in 1850 was nearly equal that of today, though it did not count as much in figures. Wages paid to ordinary workmen were from $1.25 to $2 per day. Sometimes foremen and specialists, such as hand railers, would receive from $2.25 to $3, but this was a rare occurrence. There was as much rivalry in taking jobs of work in those days as today. Every ambitious workman wanted to be a contractor….”

Figure 4. Bench planes from the Kraus tool chest including two German horn-style planes.
The expected contents of a tool chest are also included in the book:
“In those days a journeyman’s full tool chest was quite a costly investment, and many a man found it an expensive undertaking to supply himself with all the tools he needed. Besides his ordinary bench and everyday working tools, he was obliged to carry a lot of odd tools that are not thought of these days. Sash planes, match planes, moulding planes, beading planes, coves, rabbits, side filisters, try and other squares, mortise gage, and three or four other squares, bevels, miters, and half a dozen or more saws of various kinds, including a dove-tailing saw—a saw which is now almost extinct—plumb-bob, and two or three dozen chisels, gouges, and many other things the modern carpenter never wants or thinks of. The moving of tool chests was quite a big job, and the chest itself was a fearful and wonderful combination of usefulness, clumsiness and adaptability. I keep mine as a “mechanical relic,” now over sixty years old.”
Figure 5. Measuring and marking tools from the tool chest.
The Tools of John Erhard Kraus The tool chest itself is constructed from a single wide board 22-inches wide by 7⁄8-inch thick dovetailed curly maple with a mahogany panel in the lid (see cover). On the outside, Kraus added more 7⁄8-inch curly maple to simulate the frame-and-panel construction of the chest. The frames are trimmed with mahogany molding. The overall finished size of the chest is 40-1⁄4 inches wide x 25-3⁄4 inches deep x 23-1⁄2 inches high. The inside is unfinished and has three tool tills in the base and side brackets mounted for three sliding tills above the base. Only one sliding till remains with the chest, and it appears to be a partitioned tray constructed of dovetailed 3⁄8-inch thick mahogany. The supports for the sliding tool tills appear to be cherry. The chest is massive, weighing in at 125 pounds when empty. Moving the chest over the generations has caused a crack to develop in the back and one side of the chest. The original handles on the sides have also been replaced with newer ones. The chest lock, with the key still present, seems to be original hardware along with the brass hinges.
The back storage space in the bottom of the chest was designed to store the wooden molding planes and still contained twenty hollows and rounds all made by D.R. Barton & Co. in Rochester, New York (Figure 2). The back storage row also contained five sizes of beading planes ranging from 3⁄16- to 7⁄8-inch (two from D.R Barton & Co., two from Sandusky Tool and one from Auburn Tool) and two sizes of skew rabbet planes, a 1‑inch wide from G.W. Denison, and a 1-1⁄2-inch wide from D.R. Barton & Co. (Figure 3).
The front section of the chest base was designed to hold five saws, but these have all unfortunately vanished over the years. The center section of the base holds the wooden bench planes, including two toted fore planes (22 inches), one toted jack plane (16 inches), two German horn-style smoothers, a rectangular German smoother, and three sizes of American coffin smoothers in different sizes (Figure 4). There is also a D. R. Barton & Co. two-iron, 1-1⁄4-inch nosing plane and a Sandusky Tool thumbnail pattern casing plane.
Finally, there is a D.R. Barton & Co. toted beech plow plane with boxwood screws and fence. Three of the original irons for the plow plane remain in the chest. Two other plow irons appear to be well used replacements, suggesting the Kraus used the plow often for quarter-inch and half-inch applications.
In all, twenty-six of the thirty-nine planes in the tool chest were made by D. R. Barton and Co., a large, well-respected edge-tool company during the period when the chest contents were purchased. The Barton & Co.’s five-pointed star inside a half circle mark on four of the larger planes, including the plow plane and one fore plane, suggests a manufacture date of 1874 to 1880.(4)
There are no complex molding planes in the chest. Kraus may have used the hollows and rounds in conjunction with his other planes to prepare any molding shapes needed, or the planes were not stored inside the chest and have been lost over time.
Aside from the large assortment of wooden planes, the next category that is well represented is measuring and marking tools (Figure 5). The chest contains two boxwood folding rules (one from Upson Nut Co.), and a thin, 6-foot folding steel rule made by an unknown German company. There are also four framing squares. Three are 2-foot size, two of which are from Eagle Square Co. and the other an inexpensive unlabeled one, and a single 1-foot Hart Manufacturing Co. framing square. There are also two try squares. One is a T.E.Wells & Co., Sheffield, 11-inch size, and the other is a small 4-1⁄2-inch try-square/bevel combination with the 1869 Winterbottom patent date stamped on the handle.
For layout work, Kraus had two micro-adjustable steel dividers—a 5-inch and an 8-inch. Four mortise gauges are in the chest, varying in quality from a nice boxwood gauge with brass micro-adjustment thumbscrews, to inexpensive beech gauges with wooden adjustment thumbscrews. None of these had obvious manufacturer markings.
Completing the layout tools are two bevel gauges, a 10-inch manufactured by Star Tool with an 1867 patent date and an unmarked 12-inch size. There is also a short punch or awl with wooden handle, which I assume was for marking.
Figure 6. Drilling and boring tools.
Boring and drilling tools include two 10-inch sweep braces—one from John S. Fray with a Spofford stamp and an 1880 patent date and one unmarked (Figure 6). (Spofford patented a sweep brace patent in 1880 and his name was stamped along with the manufacturer on the braces from that period). There are a range of center bits, two spoon bits, a countersink, two tapered reamers, and some screwdriver bits. The chest also contains a range of double-spiral augers and an expansive bit marked “Wm A Clark.”
Two large diameter augers, a 1-1⁄2-inch and a 2-inch, appear to have been used for structural post-and-beam framing. The National Builder article noted,
“In the country nearly all the buildings were framed out of heavy timbers and the mortises and tenons were made by hand, and it was quite a job to beat a 2-inch mortise through a 10 or 12-inch timber and do it well. The whole work was done on the ground and put together with pins, which were driven tight through tenon and mortise. When ready a lot of men, neighbors generally, were invited to assist in raising the whole framework to its place, and it was then the framers came in for an impartial criticism. If the work went up easily and without a hitch, the boss was a “capital framer,” if not, the Lord help him.
“…Two augers were required, a 2-inch and a 1-1⁄2-inch one. The large one for boring the mortise, and the other for draw boring for the pins or pegs.”(5)
The writer or editor of the 1914 story may have made an error in the last sentence. A 1-1⁄2-inch diameter bit for pinning the tenons would have been too large. The 1-1⁄2-inch size may instead have been used for mortising beams of hardwood while the larger 2-inch bit would be used on softer wood. The pin diameter would typically have been more like 1 inch or slightly less.
Figure 7. Screwdrivers, chisels, cold chisels and a wrench contained in the chest. The short metal item oriented in the lower center of the picture next to the nail set is the steel “A. Kraus” stamp used to identify his tools.
There are also two T-auger handles in the chest. One has a 24-inch long, 1-inch diameter, double-spiral bit mounted. The other handle has no bit mounted, but there is an 18- inch long screwdriver bit that seems to be suitable for that T-auger handle.
The three more standard screwdrivers with handles range from very large to very small (Figure 7). The longest is a huge 21-3⁄4-inch size followed by a 16-3⁄4-inch length and a small screwdriver, 5 inches overall in length. This small screwdriver is one of only two Stanley labeled tools in the chest and has a June 6, 1871, patent date. The other Stanley item is a 1-3⁄8-inch wide plane iron, with no slot for a chip breaker, that is not mounted in a plane.
Figure 8. Hammers, cutting and shaving tools, clamps, file, saw set, and sharpening stone used by John E. Kraus.
The selection of chisels in the chest is less than would be expected for his profession. There are four mortise chisels ranging from 1⁄8-inch to 3⁄8-inch wide. There are also two firmer chisels—1⁄2-inch and 1-1⁄2-inch wide—and three gouges, a 3⁄4-inch, 1-inch, and 1-1⁄4-inch wide. Three cold chisels and a nail set are also in the collection.
Tools used for cutting belonging to Kraus that still remain in the tool chest are a draw knife with a 9-inch blade marked “Geo. Parr, Buffalo,” a lathing hatchet with a 2-1⁄2-inch-wide blade manufactured by C. Hammond, Philadelphia, a nice un-labeled spoke shave with a brass wear plate and brass adjustment thumbscrews, and a pair of Peck Stow Wilcox Co.’s no. 8 tin snips (Figure 8).
Remaining bench tools included three hammers, including one early claw hammer; an adjustable Coes wrench marked with July 1880 and 1884 patent dates; a 12-inch file marked “Eagle Works, Sheffield”; an A. Stillman saw set with a patent date of 1848; four 2-1⁄2 inch C-clamps that appear to be hand forged; and inside a wooden box, an oil stone for sharpening.
Figure 9. “Mystery tool” contained in the chest, with an adjustable metal frame, pointed on one side, attached to a central wood bar with a wooden knob and brass end stop. Inset shows verso.
There is also one “mystery tool” in the chest (Figure 9). This “whatsits” appears to be a layout jig of some sort consisting of a metal expandable frame with ten sharp points on the back which are positioned to form a rectangle 2 inches wide by 3-1⁄2 inches long. A central 8-inch long wooden bar runs through the center of the tool with a nicely turned wooden knob mounted on the wooden bar on the side of the frame away from the sharp points. There is also a brass stop screwed into the far end of the wooden central bar. The width of the frame can also be adjusted slightly between 2 and 2-1⁄4 inches.
The last “tool” belonging to Kraus is his workbench (see cover). It is a classic woodworking bench with a wooden screw front vise and a metal screw dovetailed end vise. Both of the original handles for the vises have gone missing. The dimensions are 771⁄2 inches wide x 26 inches deep x 321⁄2 inches high. The top is about 23⁄4 inches thick and has no “tool tray” feature included in the back. The workbench top is located to the base by four pins, allowing the top to be easily removed for moving the bench to different work sites. The base frame also has wedged-through tenons to allow it to also be dismantled if needed. A shelf made from a wooden packing case for “Unfermented Grape Juice” bottles was added by Kraus or possibly by his son. The bench still has two metal bench dogs included for clamping. This workbench has seen much use over the last 130 years or so, functioning as the family workbench for subsequent generations. There is a great deal of spilled and dripped old paint to clean off before the vises and bench dog holes can again work smoothly. One of the Kraus’s descendants, probably as a child, also had a fine time using the “A. Kraus” steel name stamp to emboss the end vise twenty or so times.
While the tool chest contains a large number of the original tools, it is certainly not the complete set of tools that Kraus would have needed for his profession. Com-paring the contents with the description of typical chest contents presented earlier from the National Builder 1914 article, some of the missing elements can be identified. The most obvious missing items are the five saws that had their own tool till area in the bottom front of the tool chest. In addition, a plumb-bob, a level, and mallets would have been essential tools, as well as a much larger assortment of chisels and gouges. These seem to be the type of tools that a descendant may have removed from the chest at some point in time for personal use and became mixed in with another set of household tools. There may also have been additional wooden planes, such as sash planes or more complex molding planes. If they had ever been present, they would probably have been stored outside the tool chest or been passed on to fellow professionals upon his retirement.
Summary Looking over the working tools of John Erhard Kraus, several conclusions can be drawn. Kraus’s choice of curly maple and mahogany for his tool chest attests to his pride in his woodworking skills. The chest is a step up from the more common pine tool chests that are often seen for carpenters and contractors. When it was first completed, the chest would have made an impressive statement to co-workers and customers.
Kraus selected quality tools suitable for a profession-al. They are certainly not the finest in quality available at that time, but provide a good compromise of quality and cost that one would expect from the frugal craftsman. It appears that he was willing to try to glue a crack in a coffin smoother plane, owned and possibly discarded by a D. F. Einer, although the repair was never quite completed. One plane also has an insert mortised into the sole to narrow the mouth and extend the life of the plane. A second plane was mortised for a similar patch, but the repair was never completed. Kraus seemed to be trying to get the most life out of good tools.
The tools are well cared for. Other than the Coes adjustable wrench and one mortise chisel, which have taken a beating at some point in time, the tools show little indication of mistreatment. The draw knife, for example, does not show signs of being hit with a hammer or mallet for use like a small froe, a condition I have often seen when examining antique draw knives.
The tools do, however, show that they had been heavily used. This is particularly apparent for the bench planes, the try squares, bevels, and his best mortise gauge. The result is tools that are not as pretty as some I have seen, but they do have character.
The patent dates marked on the tools range from 1848 to 1884. There is also no indication that he had switched from using the wooden planes of his youth and early adulthood to metal body planes even as they became more common.
Conclusion John Erhard Kraus died at age 73 in 1915. Was he successful at his chosen profession as a contractor? He was able to provide a living as a craftsman for himself, his wife, and his son (his daughter died before adulthood). He was able to send his son on to college at Syracuse University. That son, Edward Henry Kraus, later received a doctorate from the University of Munich in 1901 and went on to become a Dean of the College of Literature, Science and the Arts at the University of Michigan, where the Natural Science Building now bears the Kraus name, and one of the founders and then president of the Mineralogical Society of America. Kraus’s grandson, John D. Kraus, became a professor at Ohio State and an international authority on antennas, electromagnetism and radio astronomy. His two great-grandsons are a physician and a staff member at the University of New Hampshire. Certainly, this is a successful legacy for a German immigrant woodworker who first landed in an unfamiliar country in 1869. His descendants clearly had a fondness for Kraus as they have so carefully preserved the contents of his tool chest and workbench through moves from Syracuse to Ann Arbor, to Columbus, Ohio, and now into my custodianship near Boston.
My goal, after completing my research into the past of this chest and the man, is to once again put the tools back into use. A frugal man like John Erhard Kraus would, I think, be pleased.
References 1. History and Directory of the Salem Evangelical Church (W. J. Merle and C. H. Unkauf Publishers, 1907). Collection of the Onondaga Historical Association, Syracuse, N.Y. 2. Boyd’s Syracuse City Directory, (Syracuse, N.Y.: Andrew Boyd, 1873 to 1901). 3. “Memories of Fifty Years Ago in the Building Trades”, by A Retired Carpenter, The National Builder (January 1914): 104-106. 4. Frank Kosmerl, “Rochester, New York, A Nineteenth-Century Edge-Tool Center, Part V: David R. Barton,” The Chronicle, 53, no. 1 (March 2000): 13-25. 5. “Memories of Fifty Years Ago in the Building Trades,” 105.
Author Jeffrey Neil is a full-time staff scientist at OSRAM Sylvania in Beverly, Massachusetts, and a part-time amateur woodworker. His interest in using antique tools was initiated after taking two classes in chairmaking at Mike Dunbar’s Windsor Institute. He hopes he can resist the temptation to become a tool collector and concentrate on building. His wife, Darlene, whose quilting contacts led to the discovery of this tool chest can now attend as many quilting “camps” as she likes.
Comments